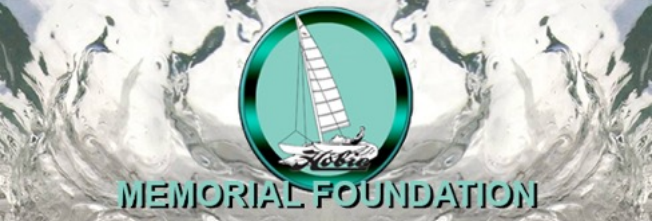
The Hobie Memorial Foundation is raising funds to construct a memorial honoring Hobie Alter’s life and his many contributions to the surfing, boating, and skateboarding industries. The Hobie Memorial Foundation Newsletter publishes fascinating historical accounts such as this one in every issue.
“Mr. Hobie, would you have a job for me?” thirteen year old Jimmie Lomas asked Alter on his third visit to the newly opened surf shop in Dana Point.
“Yeah, I do! Here’s the broom, here’s the dustpan, there are 50-gallon drums out back,” Hobie replied, looking around. “All of this on the floor goes in those drums, and if you find any tools, put them over on the work bench and I’ll show you where they go later.”
Without hesitation, Hobie hired his first employee. Jimmie Lomas was the shop janitor.
Young Lomas had been watching as the first surfboard shop in Dana Point was being constructed on the nearly empty Pacific Coast Highway. The only other building on that side of PCH was architect, Glen Muir’s building across from La Plaza. “It wasn’t like there was much happening in Dana Point back in 1953,” remembered Lomas, who moved to town with his family six years earlier.
RELATED: Those Ruffian Surfers and the 1953 Surf Ban
“For fun, my friends and I used to climb down the hill from the lookout to the old pier that sat on railroad tie pilings. Over on the east side of Dana Point, we didn’t have as much freedom. Scouting around Selva where the Irvine Ranch started, we weren’t allowed out alone in the evenings without an adult because of mountain lions. We’d see their paw prints down in the washes. They definitely weren’t kitty cats!”
Cleaning up the surf shop, which was solely manufacturing, Lomas realized that Hobie made the boards all by himself. “It was just Hobie. He shaped and sanded the balsa,
then glassed and glossed them. Every surfboard that left his shop in the beginning was hand made by him.”
Hobie was also patching boards. “When he started taking in a lot more boards with dings, he showed me how to patch. Once he saw that I had the skills with my hands and eyes, he said, “Okay, you’re the patcher.” That’s when he got somebody else to sweep the floors.”
Phil Edwards came on board in 1955 sanding the planer marks out of boards. “A very time-consuming part of shaping balsa surfboards is sanding the final finish before glassing,” Lomas explained. “You have to sand those Japanese planer marks out of the board without digging holes, because you’ve got planks glued together that are different densities. So you really had to be skilled. You had to use your eyes, your hands, you had to be a natural born craftsman.”
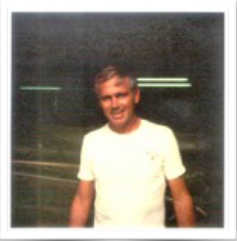
“Phil would drive up from Oceanside, stay overnight, surf, visit his girlfriend, then he’d go back home. Although he wanted to shape, Hobie wouldn’t let him. So he quit and started building boards down in Oceanside.”
“Come here, Lomas,” Hobie said one day. “I want to see if you can sand the planer marks out.”
“I got promoted. Obviously, I could do it.”
Jimmy Jones was initially hired to glass Hobie’s boards, but he left and a young Laguna surfer, Renny Yater, stepped in. Renny was a true waterman. During abalone season in the Spring, he dove professionally until the coast got pretty much picked over, then during lobster season beginning in October, he trapped bugs. The remainder of the year Yater glassed for Hobie. As Hobie’s shop got busier, balsa became more scarce. The aircraft industry was starting to use balsa because of the success of the balsa sandwich construction used in aircraft. Hobie’s competition, Velzy and Jacobs were also using a lot of the lightweight wood.
“I showed up for work one day in the Fall of 1956,” said Lomas,” and Hobie said, “I’m not gonna need you around here for a few months. Me and Gordon (Gordon Clark, eventual owner of Clark Foam) are gonna work on something.” When I came around again in March or April, the two men had developed isocyanate foam for surfboard blanks. The foam creates unbelievable pressures when it is expanding.”
In the beginning, Hobie’s foam surfboards weren’t perfect, according to Lomas. “They had pockets of air in the finished shape. We’d have to chip the holes out. We’d fill them with resin and Bakelite, and then we’d have to resin and sand them before they were glassed. It was kind of labor intensive. The foam eventually got perfect.”
Building foam versus balsa cut the finish sanding of the shaped board out of the process completely. The shaper was now responsible for finishing the board.
Joe Quigg was the first shaper Hobie hired. Renny wanted to shape, but Hobie wouldn’t let him either, so he too quit and went down to Velzy’s in San Clemente. Ralph Parker, who was also hired, went on to become his top shaper for years.
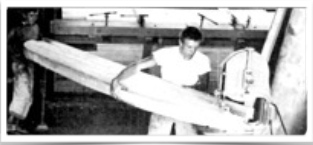
When production got going, Hobie moved to a building on Domingo in Capistrano Beach that he bought specifically for shaping, sanding, glassing, and glossing. Before long, production grew again. They didn’t have enough room so he rented the building across the alley.
By that time, Joe Quigg moved up to Newport Beach to shape. Hobie had hired a handful of shapers, the well-known Terry Martin, Ralph Parker, Phil Edwards who had his own model, John Gray, and Del Cannon. Velzy even shaped occasionally for Hobie after he went out of business.
“I began glassing back in Dana Point, alongside Bing Boca. Bing was a young Laguna guy and a great athlete. He was the only guy around that could beat “Black Butch” Van Artsdalen in a paddling race.”
Lomas and Boca were also making their own fins. “We had to cut the fins out on a band saw, out of three-quarter inch thick by ten-inch wide mahogany. I’d take these big long pieces of wood in my 1944 Ford Sedan Delivery to school and cut the fins out. I was a star in wood shop at Old Capo High. At parents’ night, I made the wood shop teacher look awfully good because I built some pretty nice pieces. Bing’s wood shop teacher also let him cut fins out in class. Those were the good old days.
We then had to hand-shape the foil on the fin. They were all just wooden fins glassed on. On foam boards too. Because the bottom had already been glassed, we’d put two nails in them and cut the heads off. You didn’t do this while you were glassing the bottom. It’s a separate operation. We shaped the foil with a disc sander the way Hobie showed us, which was using a five-gallon bucket turned upside down and holding the fin with our foot. It was skilled. I mean, this was all free hand.
Once we moved over to Capo Beach, Bobby Patterson and Brian “The Sparrow” Test were
hired to glass,” recalled Lomas, “and the Dana Point store became strictly retail and patching.”
Eventually, Lomas moved to finish sanding the glassed boards. “I decided I really wanted to become proficient at all of it, which I did. I sanded for about six
to eight months with Ronald Patterson, who was our key sander. If there were fifteen boards, he sanded ten because he was married. I only got five.”
Lomas worked for Hobie for over twenty years with only a short break away when he was hurt in a serious motorcycle accident racing in a scrambles race at the
Perris scrambles track. Undergoing three operations, and in a cast from his crotch to his toes for seven months, he was hired by Fred Carrillo of Carrillo Connecting Rods, connecting rods for racing engines.
During this time, Hobie was building two Hobie 14’s a day in the Quonset hut behind Kenny’s Hardware in Capo Beach. A year and a half later, Lomas was invited to Hobie’s Christmas Party.
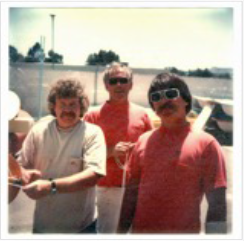
Called into another room by Hobie and Sandy Banks, he told Lomas. “We’re breaking ground in San Juan on our first plant and we’re gonna need a whole lot of production molds. I have some innovative ideas on mold making.”
“These were the molds for the Hobie 14,” explained Lomas.
Meanwhile, Hobie brought Phil back from Hawaii and shipped his catamaran, the El Gato II home to Capo Beach. He was ready to start on the Hobie 16. The two men proceeded to draw out new plans in the sawdust on the floor of the Quonset hut, and out of those renderings they produced three prototypes. “Phil’s a hell of a craftsman. What an eye!” said Lomas. “Phil and I shaped and glassed the first foam plugs for the Hobie 16. Hobie checked in on us on his return trips. We were cooking!
Everything was running real smooth. Building boats; the 14s, the 16s were just taking off. I think it was the best boat we ever built. It was just a hell of a boat.
I was at our local eatery and watering hole one evening, the Captain’s Anchorage, and Teddy Birman was talking about the new mold shops that they were breaking ground on. And I said, “What the hell are you talking about?”
Teddy said, “Well, we’re building two new mold shops!”
I said, “Really? What are you gonna put in them for molds? Nobody’s told me what’s going on!”
Teddy’s mouth hung open and he said, “Oh my God!”
They completely overlooked telling the tooling department. I had to quickly come up with 22 sets of molds. When Hobie realized I hadn’t been told, he said, “You’re gonna have to run two shifts.”
Probably my greatest achievement at Hobie Cat was having all those molds ready to go when they finished the mold shops.
It was 1977 when Lomas finally left Hobie. “It was kind of cool working for him all those years because I wasn’t in the limelight. I was hidden, which I thought was great. I didn’t have a bunch of people gawking at what I was doing and getting ideas.”
Lomas went on to do some work in Hollywood for a while, and is now retired and living in Tustin, California.